As far as the current status of ball screw processing is concerned, commonly used ball screw processing technology methods can be mainly divided into two categories: chip processing (cutting and forming) and chipless processing (plastic processing). The former mainly includes turning, cyclone milling, etc., while the latter includes cold extrusion, cold rolling, etc. In view that most customers are not very familiar with ball screw processing technology, the following is a brief analysis and explanation of the characteristics, advantages and disadvantages of these two ball screw processing technologies.
Introduction to commonly used ball screw processing technology methods:
1. Chip Processing
Screw chip processing refers to the use of cutting and forming methods to process the screw, mainly including turning and cyclone milling.
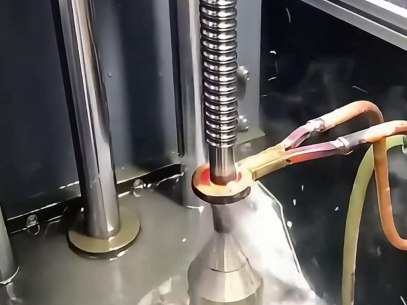
Turning: Turning uses different turning tools or other tools on a lathe. It can process various rotating surfaces, such as internal and external cylindrical surfaces, internal and external conical surfaces, threads, grooves, end faces and formed surfaces, etc. The processing accuracy can reach IT8-IT7. The surface roughness Ra value is 1.6~0.8. Turning is often used to process single-axis parts, such as straight shafts, discs, and sleeve parts.
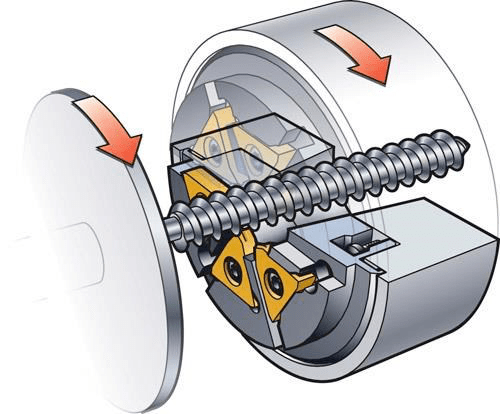
Cyclone cutting (whirlwind milling): Cyclone cutting (whirlwind milling) is a high-efficiency thread processing method, suitable for rough processing of larger batches of threads. The process is to use a carbide cutter to mill the threads at high speed. It has a tool The advantages of good cooling and high production efficiency.
2. Chipless Processing
Chipless processing of screw rods refers to processing screw rods using metal plastic forming methods, mainly including cold extrusion and cold rolling.
Cold Extrusion: Cold extrusion is a processing method in which the metal blank is placed in the cold extrusion die cavity, and at room temperature, the fixed punch on the press is applied to the blank to cause plastic deformation of the metal blank to produce parts. At present, the general dimensional accuracy of cold extrusion parts developed in my country can reach 8~9 levels.
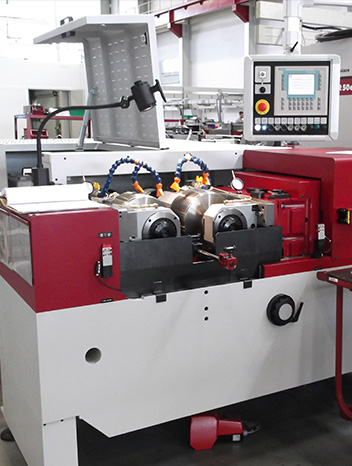
Cold Rolling: Cold rolling is made from hot-rolled plates at room temperature. Although the steel plate will heat up due to rolling during the processing, it is still called cold rolling. The cold rolling forming process of the ball screw threaded raceway is the friction force formed between the roller and the metal round bar. Under the push of the spiral pressure, the metal bar is bitten into the rolling area, and then the forced rolling force of the roller acts the process of plastic deformation.
Comparison of the pros and cons of commonly used ball screw processing techniques:
Compared with traditional cutting machining, the advantages of chipless machining are:
1. High product performance. Using cutting processing methods, due to the tearing of metal fibers and low surface quality, it is generally necessary to increase the grinding process. Chipless machining uses plastic forming method, cold work hardening occurs on the surface, the surface roughness can reach Ra0.4~0.8, and the strength, hardness, and bending and torsion resistance of the workpiece are improved.
2. Improve production efficiency. Generally, production efficiency can be increased by more than 8 to 30 times.
3. Processing accuracy is improved. The processing accuracy can be improved by 1 to 2 levels.
4.Reduced material consumption. Material consumption is reduced by 10%~30%.
For more information, please contact us at amanda@kgg-robot.com or +WA 0086 15221578410.
Post time: Nov-12-2024