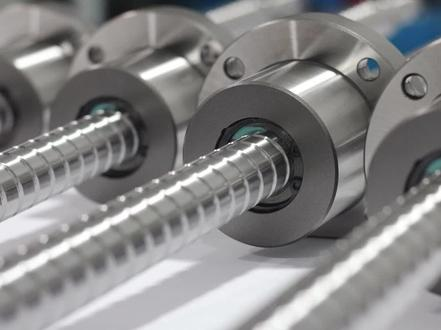
In modern automated production lines, ball screws have become an important transmission component for a wide range of applications due to their high precision and efficiency. However, with the increase of production line speed and load, the noise generated by ball screws has become a problem that needs to be solved. Reducing noise pollution from ball screws not only enhances the comfort of the working environment, but also improves the service life of the equipment and the overall efficiency of the production line.
Ball screws use recirculating ball bearing elements and there is inherent noise in the movement of these elements around the screw and through the nut, but there are steps you can take to minimize the noise as much as possible:
Design optimization is the first step in reducing ball screw noise. The structural design and manufacturing accuracy of a ball screw has a direct impact on its operating noise. By optimizing the screw's helix angle and ball diameter, you can effectively reduce friction and collision and reduce noise.
Material selection also plays an important role in noise control. The main components of a ball screw include the screw, nut and balls. Selection of high-strength, low coefficient of friction materials can effectively reduce noise. The use of high hardness alloy steel or ceramic materials for ball screws can reduce the noise generated by friction and collision.
At the same time, the surface of the nut and screw is precision machined and surface treated, such as chrome plated or oxidized, which can further reduce the coefficient of friction, improve the smoothness of operation and reduce noise.
Lubrication is one of the key factors to reduce ball screw noise. Good lubrication can form a lubrication film between the screw, nut and ball, reducing direct contact and friction, thus reducing noise. Choosing the right lubricant is very important. Lubricants have good fluidity and heat dissipation and are suitable for high-speed, high-load working environments. Grease, on the other hand, is suitable for low to medium speeds and lower loads, and has good adhesion and sealing properties.
In modern automated production lines, automatic lubrication systems, such as oil and gas lubrication or micro-lubrication technology, can be used to ensure uniform lubrication of ball screw components and reduce friction and noise by controlling the lubricant supply volume and supply position.Whether it is oil lubrication or grease lubrication, it is necessary to choose according to the specific working conditions and environment of the ball screw, and regularly check and replace the lubricant to maintain good lubrication effect.
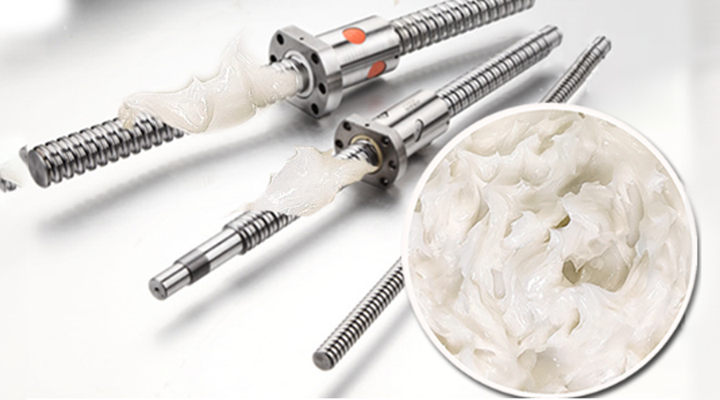
The use of the environment on the ball screw noise impact should not be ignored. Dust, particles and moisture and other impurities in the working environment can easily enter the inside of the ball screw, increasing friction and wear, thus generating noise. Therefore, it is necessary to take effective measures against dust, dirt and moisture to keep the working environment clean and dry.
Maintenance is a long-term measure to reduce the noise of ball screw. Regularly checking and maintaining the operation status of ball screws, and finding and solving problems in time are important means to reduce noise.
Reducing the noise pollution of ball screws in automated production lines is a comprehensive issue involving design optimization, material selection, lubrication, use of the environment and maintenance and other aspects. By optimizing the design and manufacturing process, selecting high-performance materials, adopting advanced lubrication technology and measures, maintaining a good use environment, and carrying out regular inspections and maintenance, the noise of ball screws can be effectively reduced, and the overall performance of the automated production line and the comfort of the working environment can be improved.
Post time: May-27-2024