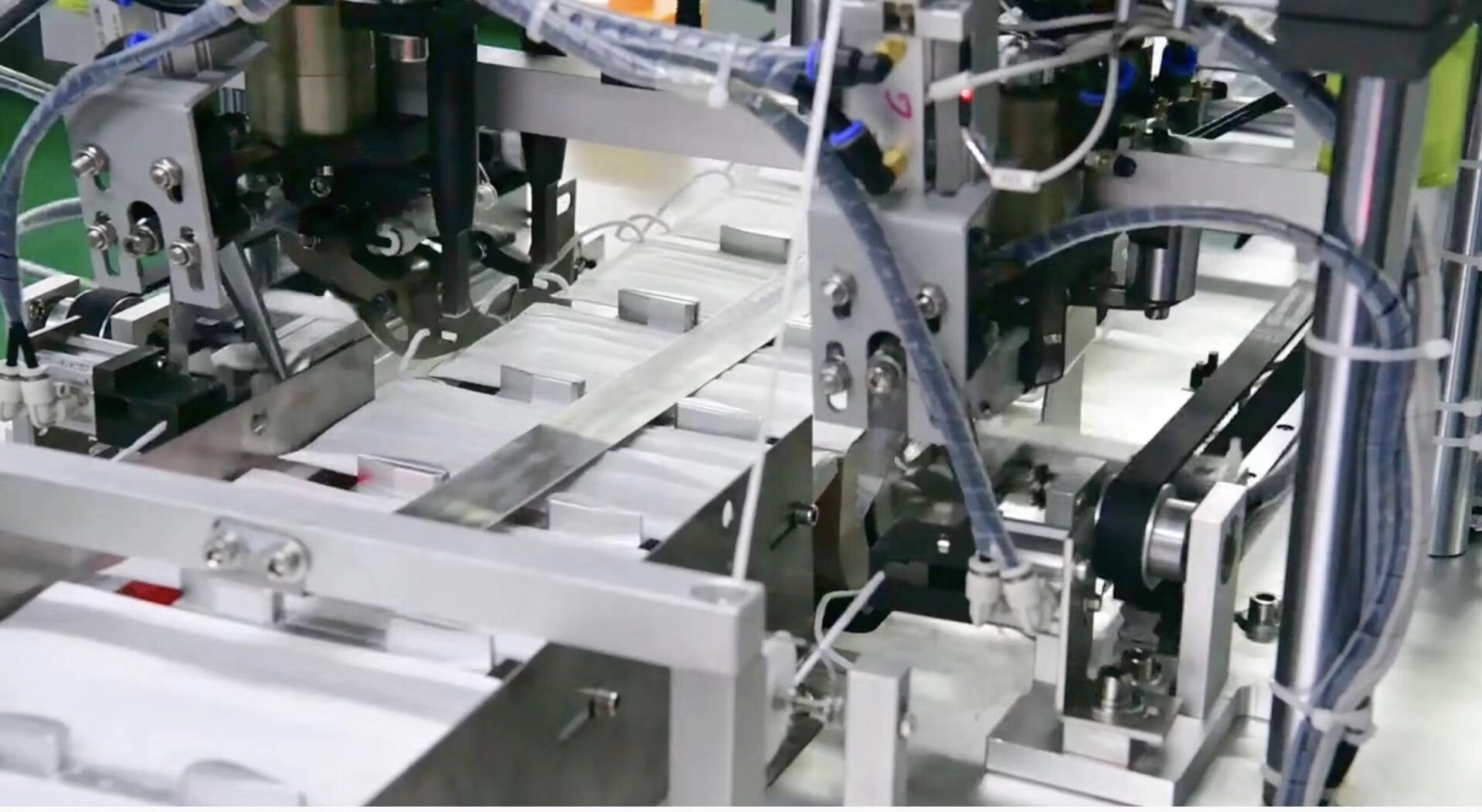
With the development of digital control technology, most of the motion control systems use stepper motors or servo motors as execution motors. Although the two in the control mode is similar (pulse string and direction signal), but in the use of performance and application occasions there is a big difference.
Stepping motor&Servo motor
The control of different ways
Stepping motor (an angle of a pulse, open-loop control): the electrical pulse signal is transformed into an angular displacement or line displacement of the open-loop control, in the case of non-overload, the motor's speed, the position of the stop only depends on the frequency of the pulse signal and the number of pulses, without the influence of the load change.
Stepper motors are mainly classified according to the number of phases, and two-phase and five-phase stepper motors are widely used in the market. The two-phase stepping motor can be divided into 400 equal parts per revolution, and the five-phase can be divided into 1000 equal parts, so the characteristics of the five-phase stepping motor are better, shorter acceleration and deceleration time, and lower dynamic inertia. The step angle of two-phase hybrid stepping motor is generally 3.6°, 1.8°, and the step angle of five-phase hybrid stepping motor is generally 0.72°, 0.36°.
Servo motor (an angle of multiple pulses, closed-loop control): servo motor is also through the control of the number of pulses, servo motor rotation angle, will send out the corresponding number of pulses, while the driver will also receive the feedback signal back, and the servo motor to form a comparison of the pulses, so that the system will know the number of pulses sent to the servo motor, and at the same time how many pulses received back, will be able to control the rotation of the motor very accurately. The precision of the servo motor is determined by the precision of the encoder (number of lines), that is to say, the servo motor itself has the function of sending out pulses, and it sends out the corresponding number of pulses for every angle of rotation, so that the servo drive and the servo motor encoder pulses form an echo, so it is a closed-loop control, and the stepping motor is an open-loop control.
Low-frequency characteristics are different
Stepping motor: low-frequency vibration is easy to occur at low speeds. When the stepping motor works in low speed, generally should use damping technology to overcome the low-frequency vibration phenomenon, such as adding a damper on the motor, or drive using subdivision technology.
Servo motor: very smooth operation, even at low speeds will not appear vibration phenomenon.
The moment-frequency characteristics of different
Stepping motor: the output torque decreases with the increase of speed, and it decreases sharply at higher speeds, so its maximum working speed is generally 300-600r/min.
Servo motor: constant torque output, that is, in its rated speed (generally 2000 or 3000 r/min), the output rated torque, in the rated speed above the constant power output.
Different overload capacity
Stepping motor: generally do not have overload capacity. Stepping motor because there is no such overload capacity, in order to overcome the selection of this moment of inertia, it is often necessary to select a larger torque of the motor, and the machine does not require so much torque during normal operation, there will be a waste of torque phenomenon.
Servo motors: have a strong overload capacity. It has speed overload and torque overload capability. Its maximum torque is three times the rated torque, which can be used to overcome the moment of inertia of inertial loads in the start-up moment of inertia.
Different operating performance
Stepping motor: stepping motor control for open-loop control, start frequency is too high or too large a load is prone to lose steps or blocking the phenomenon of stopping too high a speed is prone to the phenomenon of overshooting, so in order to ensure the accuracy of its control, should be dealt with the problem of rising and falling speed.
Servo motor: AC servo drive system for closed-loop control, the driver can be directly on the motor encoder feedback signal sampling, the internal composition of the position loop and speed loop, generally does not appear in the stepping motor loss of steps or the phenomenon of overshooting, the control performance is more reliable.
Speed response performance is different
Stepping motor: accelerate from standstill to the working speed (generally several hundred revolutions per minute) requires 200 ~ 400ms.
Servo motor: AC servo system acceleration performance is better, from standstill accelerate to its rated speed of 3000 r/min, only a few milliseconds, can be used for the requirements of rapid start-stop and positional accuracy requirements of the control of the high field.
Related Recommendations: https://www.kggfa.com/stepper-motor/
Post time: Apr-28-2024